Processors Turn to Gear Pumps to Boost Extruder Output and Meet Surging Manufacturing Activity (August 2, 2022)
PSI-Polymer Systems Inc. Sees Big Upsurge in Orders as Processors Get Creative in Meeting Extrusion Production Demands
CONOVER, N.C., August 2, 2022 – With heightened capacity demand and extended lead times for production equipment including extruders, processors have turned to gear pumps as a solution to boost productivity and meet the nation’s surging manufacturing demands, according to PSI-Polymers Systems Inc. (PSI), a leading global supplier of high-performance gear pumps, screen changers, custom auxiliaries, and rebuilds for the polymer, adhesive, chemical, and food processing industries.
Over the past two years, PSI has experienced a massive upsurge in orders for gear pumps due in large part to scarcity of new extruders which have experienced lead times up to 50-plus weeks. Similarly, used extruders have been snapped up and processors left scrambling to find ways to meet demand, according to Don Macnamara, general manager of PSI-Polymer Systems Inc. “Extruder production is at maximum capacity, labor is scarce, and with an increase in turnover, processors are using every available resource and thinking creatively to manage increased backlogs and retain customers,” said Macnamara. “Excessive backlogs and longer lead times can result in customer drift and the heightened potential for long-term loss of valued business relationships. Processors are doing all they can to boost outputs to reduce lead times. This is where the gear pump comes in.”
Typically, gear pumps are installed on an extrusion line to control profile dimensional stability and weight-per-length. However, processors now have been quick to assess and prioritize the production output gains made available by the gear pump. The gear pump assumes the pressure-generating function of the extruder and allows it to do what it does best: feed, melt, and meter, says Macnamara.
With the pressure function removed, the extruder operates at a lower head pressure. This effectively boosts extruder output by reducing backpressure induced losses in flow. According to Macnamara, older extruders often see an output gain of 18%-25%. Adding gear pumps to 4 to 5 older extruders can yield a production gain similar to that of adding a new extrusion line. New extruders see gains of approximately 10%. Output gains are dependent on material viscosity and how much material is being held back by pressure.
A gear pump will also dampen the effects of extruder pressure variation at the die by a range of 20:1 up to 50:1 depending on the process. This allows gauge/wall control to nominally +/- .25%, significantly reducing the amount of resin used per linear foot. For example, with no melt pump, a one-foot, 1.5” diameter pipe section (SDR 13.5) made toward the heavier end of the ASTM spec has a target weight of 151g (.333 lb). Adding a melt pump to the line delivers a consistently accurate profile toward the lower end of the ASTM spec at a reduced weight of 145g (.320 lb) per foot. This results in a net savings of 6 grams (.013 lb) per linear foot. At a line speed of 65 fpm, a 20/5/50 operation could realize a net annual material savings of over a quarter-million pounds per year.
“In a market where pricing is volatile and resource availability often unpredictable, reducing the percentage of material given away in the product can mean the difference between making additional shipments or looking at empty silos,” said Macnamara.
Shifting the pressure generating function to the melt pump also reduces the amp load on the extruder. Higher viscosity/fractional-melt index materials will see the greatest benefit. Lower amp load translates to lower energy costs. In most cases, adding the gear pump motor to the line reduces overall amp draw and generates significant overall energy savings. Additionally, lower extruder head pressure puts less load on the thrust bearing and gear box adding to the expected life and reducing extruder wear and tear.
# # #
About PSI-Polymer Systems Inc. Founded in 2000 by an industry veteran and backed by a dedicated team of former gear pump and screen changer business owners, PSI’s vision of systematizing process hardware between the extruder and the die quickly caught hold. Introducing technologies that incorporated proprietary and patented machine improvements, PSI challenged conventional system design and ultimately raised industry standards for performance and supply.
For polymer and hot melt adhesive filtration requirements, PSI screen changer types include Backflush (CSC-BF), Continuous dual-piston (CSC), Discontinuous single-piston (DSC), Hydraulic Slide Plate (HSC), Manual Slide Plate (MSC), and In-Line Filters (ILF). For large polymer reactor and compounding lines, PSI offers Extended Area Continuous Screen changers (EAC). Gear pump types include: Extrusion Gear Pump (EGP), High-Pressure Gear Pump (HGP), Chemical-Industrial Gear Pump (CIP), and Fluoropolymer Gear Pump (FGP) for fluorinated plastics. For more information, visit www.psi-polymersystems.com.
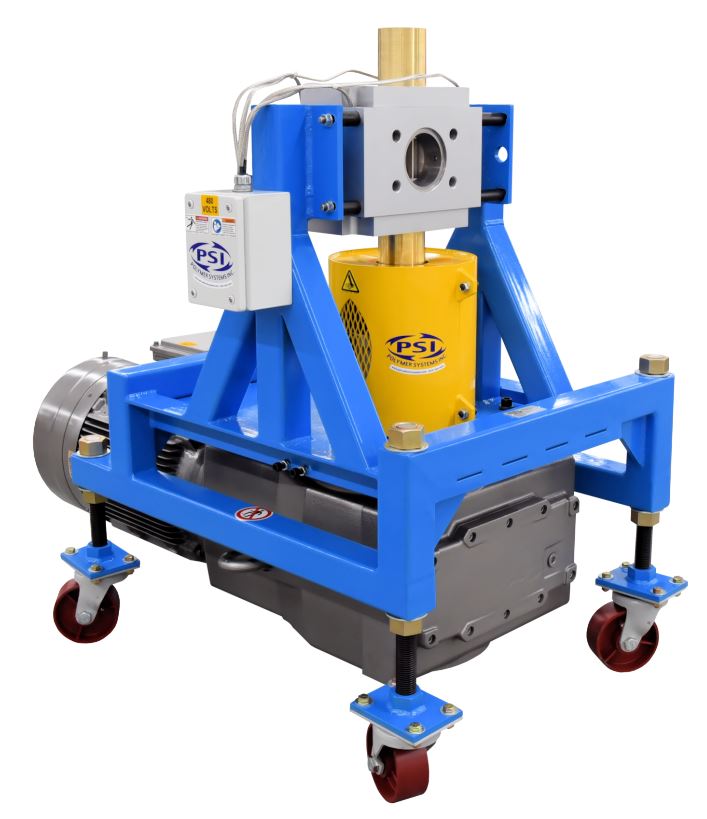