New Enhancements Help Processors Maximize Efficiency and Boost Screen Changer Performance (June 1, 2023)
CONOVER, N.C. – Faced with surging manufacturing demands, processors can employ a range of new options to boost productivity and enhance screen changer performance, according to PSI-Polymers Systems Inc. (PSI), a leading global supplier of high-performance gear pumps, screen changers, custom auxiliaries, and rebuilds for the polymer, adhesive, chemical, and food processing industries.
With heightened capacity demands and extended lead times for production equipment including extruders, processors are looking to maximize efficiency and dial-in certain enhancements to improve the overall manufacturing process, says Don Macnamara, general manager of PSI-Polymer Systems Inc.
“Processors are using every available resource and thinking creatively to manage increased backlogs and retain customers,” said Macnamara. “To get more out of the process, there are a range of tried-and-tested enhancements that will give processors a leg up in meeting their day-to-day manufacturing demands.”
Processors can wring out greater efficiencies by using Super Plates, Oval Screen Pocket, and Low Delta P Breaker Plate options. Super Plates add efficiency and life to screen packs by allowing better utilization of the surface area. Doing so reduces screen replacement frequency and cost, according to the company.
The gain is achieved by lifting the screen pack away from the flat, solid surface of the breaker plate. Conventional breaker plate open area is typically 50% to 55%. This means 45% to 50% of the screen rests on a solid surface. As a result, screen life diminishes rapidly as the small corresponding area over the breaker plate holes is blinded and the material must laterally traverse less clogged areas of the wire cloth to reach a through hole. This can be observed on spent screen packs as dense pockets of filtered contaminants over the breaker plate holes and lesser concentrations over the solid part of the breaker plate, according to PSI.
Use of a Super Plate fully exposes up to 95%+ of the screen to through-flow of the melt stream. This can yield a gain of 30-55% in effective filtration area over a conventional design.
The Super Plate is a finely machined grid of stainless-steel triangular blades, cross welded to provide superior strength and support. The screen pack rests on the edge of the blades. Spacing and support of the blades often allows the cost-saving elimination of a 20-mesh or higher support screen. The Super Plate also eliminates the risk of screen blow-through and resulting contaminants in the end product that can occur if the delta-P exceeds the tensile strength of the wire cloth sitting directly above a breaker plate hole.
Meanwhile, Low Delta P Breaker plate design can significantly impact production run times between screen changes. Every process has a high-pressure limit defined either by the extruder or the yield strength of the screen pack. Starting (clean screen) pressure drop defines the low end of the process pressure window. Since screen micron rating and related wire diameters are generally standardized, when working with a defined filtration level, the remaining variable for reducing pressure drop is the diameter of the holes in the breaker plate.
Efficient breaker plate design balances open area and yield strength to minimize pressure drop. For most polymers and adhesives processed through screen changers, the industry standard (Class 2) breaker plate hole size works well. However, for high viscosity, fractional melt materials, the typical hole diameter generates a high-pressure drop. This reduces the pressure window and corresponding run time available for a given screen pack and results in more frequent screen changes.
To reduce pressure-drop for these materials and add run time between screen changes, PSI offers Class 3 and Class 4 breaker plates, each having successively larger holes than the standard Class 2 plate. The Class 2 holes are ideally sized to support a 20-mesh screen. The larger diameter of the Class 3 and 4 holes use a Super Plate or a 10-mesh support screen for the finer filter screens.
These Class 3 and 4 breaker plates are available for CSC (continuous) and DSC (discontinuous) bolt-type screen changers and MSC (manual) slide plate screen changers.
When space and screen life are considerations, an oval screen pocket offers significant productivity advantages, according to the company. Available for bolt-type screen changers, the elongated pocket increases the filter area by roughly 168+%. This can be generally equivalent to upsizing the screen changer 1-1/2 to two times the model size but with the space envelope of the smaller screen changer.
Pressure drop across the screen pack is lower, yielding higher throughput rates given the lower average back pressure. Shear stress is lower, boosting melt integrity.
Screen life is roughly linear to the area increase, yielding an increase in time between screen changes. For processes where recycle material can contain ‘bursts’ of contaminants, the longer screen life allows the operator longer intervals between screen maintenance. This option is only available for new machines due to the custom housing and bolts.
# # #
About PSI-Polymer Systems Inc. Founded in 2000 by an industry veteran and backed by a dedicated team of former gear pump and screen changer business owners, PSI’s vision of systematizing process hardware between the extruder and the die quickly caught hold. Introducing technologies that incorporated proprietary and patented machine improvements, PSI challenged conventional system design and ultimately raised industry standards for performance and supply.
For polymer and hot melt adhesive filtration requirements, PSI screen changer types include Backflush (CSC-BF), Continuous dual-piston (CSC), Discontinuous single-piston (DSC), Hydraulic Slide Plate (HSC), Manual Slide Plate (MSC), and In-Line Filters (ILF). For large polymer reactor and compounding lines, PSI offers Extended Area Continuous Screen changers (EAC). Gear pump types include: Extrusion Gear Pump (EGP), High-Pressure Gear Pump (HGP), Chemical-Industrial Gear Pump (CIP), and Fluoropolymer Gear Pump (FGP) for fluorinated plastics. For more information, visit www.psi-polymersystems.com.
Press Contact:
Joseph Grande
J. Grande communications Inc. 413.684.2463 joe@jgrandecommunications.com
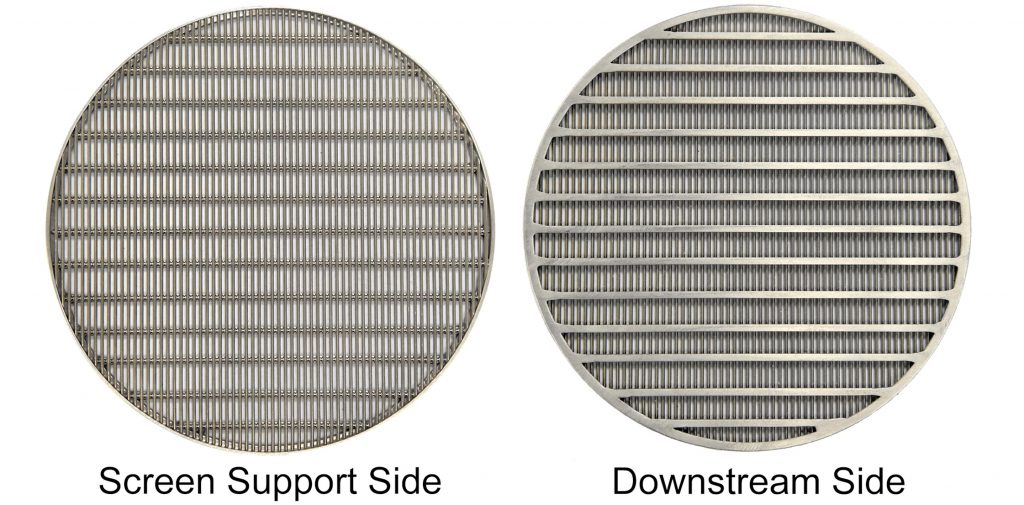
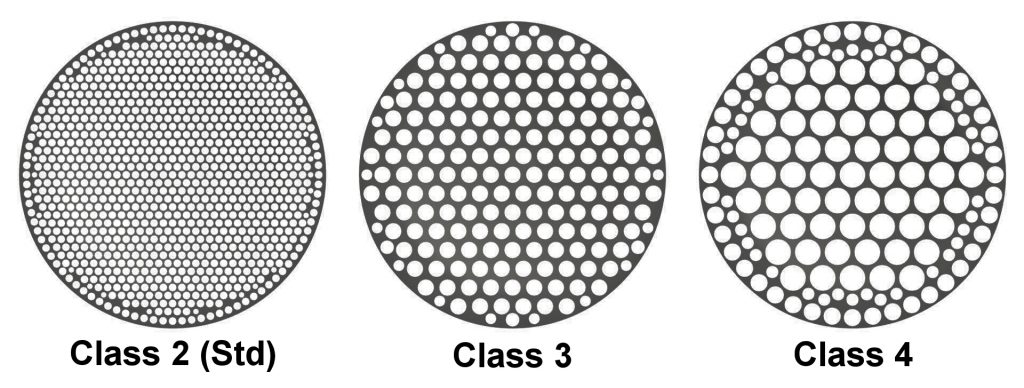
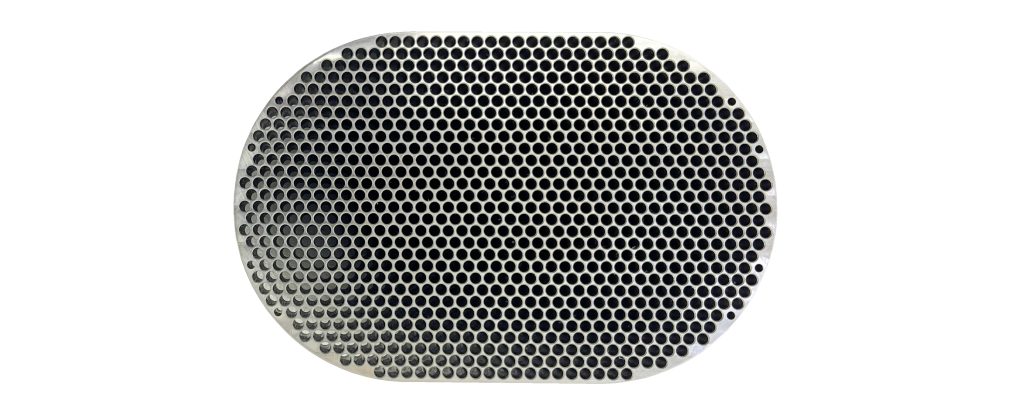